Digitalization, reduced demand for certain paper products and evolving industry challenges force pulp and paper companies globally to focus on innovation, product differentiation and, perhaps most importantly, sustainability.
Facing competition from other countries with lower production costs and more efficient supply chains, Canadian companies must balance environmental, labor and safety standards with the constant demand for improved efficiency and product quality. Given constant technological advancements and ever-evolving environmental concerns, paper chemical companies, kraft chemical and semi-mechanical pulp mills, and paper and wood mills must embrace smart monitoring for a more sustainable future.
Pulp production has, unfortunately, historically been a resource-intensive endeavor. But precisely measuring the concentration of total dissolved solids and various liquids at different steps of the process empowers decision-makers to adjust the parameters to optimize resource utilization, minimize environmental impact and enhance operational efficiency — all while maintaining the high production standards that make Canadian pulp and paper products renowned globally.
Kraft recovery
- Minimizing the environmental impact of water material (black liquor) from the pulping process.
- Recycling pulping chemicals, such as sodium hydroxide (NaOH) and hydrogen sulfide (H2S).
- Cogenerating steam and power.
Black liquor, a byproduct of the kraft process, combines removed lignin, hemicelluloses, water and other chemicals used in the extraction process. The feed to the evaporation stage should be as consistent as possible to maximize capacity and stabilize the output concentration. Feed concentration maintains consistency by regulating the mixing liquor with a process refractometer.
The separated black liquor is then sent to the evaporation stage. Evaporation is critical in chemical recovery, concentrating the black liquor for efficient pulping chemical recovery.
The concentrated black liquor from evaporation is then sent to a recovery boiler, which burns the remaining organic materials in the black liquor, generating heat to produce steam. Steam is often used to power turbines for electricity generation or heating purposes within pulp mills.
When the concentration of black liquor is maximized, so is the energy production.
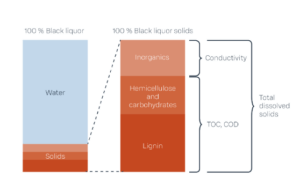
Concentrated black liquor is sprayed into the recovery boiler where it’s burned to form sodium sulfide. The inorganic sodium and sulfur are recovered as molten smelt, which is dissolved to form green liquor. The green liquor is then sent to the causticizing plant, where passive chemicals are converted into active cooking chemicals to make white liquor.
Green liquor density, or total titrable alkali (TTA), must be measured accurately in the dissolving tank and shaker feed to achieve high-quality white liquor. Real-time measurement and control of TTA density during the causticizing process reduces the risk of overliming, increases process efficiency and creates consistent and high green-liquor TTA levels for slaking, boosting white liquor quality while decreasing operating costs.
Brown stock washing
Brown stock washing (BSW) significantly impacts pulp mill economics. Aiming to eliminate most of the soluble organic and inorganic impurities in a pulp suspension (brown stock), the BSW process also helps to retrieve cooking chemicals and organics for energy recovery, steam and electricity generation while minimizing wash liquor and water consumption.
Recovered organic compounds are used for energy production and directly affect the consumption of bleaching chemicals and, therefore, the mill’s environmental load. Since recovered inorganic compounds are used to regenerate cooking chemicals, the more inorganics lost with the pulp, the greater the requirement for make-up chemicals in the recovery system. Efficient BSW improves oxygen delignification performance and subsequent bleaching stages by reducing reagent consumption (Figure 2). With more spent chemicals recovered, the plant’s effluent load is reduced.
The key to BSW is inline, real-time TDS measurements that provide accurate process data and help balance water used in washing and chemicals used in bleaching by driving quick responses to potential process changes or disturbances. Monitoring TDS requires measurements at the digester washing zone and blow line, from the pulp feed to washers, in filtrate lines during the washing stage, during pulp to oxygen delignification and pulp discharge to bleaching to maximize efficiency and quality throughout the washing process.
The transformative potential of inline monitoring in the kraft chemical recovery and brown stock washing processes is undeniable, setting the stage for reliable measurements to serve as the cornerstone of the Canadian pulp and paper industry’s ongoing commitment to sustainability.
Reliable measurements for a greener future of pulp and paper
The Canadian pulp and paper industry faces the multifaceted challenge of reducing its environmental impact while maintaining global competitiveness. Adopting inline measurement technologies throughout these processes supports the sustainability and performance requirements of more sustainable pulp production in the future (Figure 3).
Realizing a cleaner, more profitable future for pulp and paper demands collective effort, innovation and a shared vision for environmental stewardship. By fostering collaboration among mills, regulatory bodies, technology providers and academic institutions, the industry can harness the full potential of inline monitoring to drive transformative change. This united front will pave the way for Canadian mills to optimize resource utilization, minimize ecological footprints and unlock new efficiency frontiers at every production stage.
Position your brand as a champion of sustainable manufacturing with inline measurement and process control to contribute to a greener, more prosperous future for the industry and solidify our national legacy as a global leader in responsible pulp and paper resource management.
Article by Vaisala